Fire truck design trends are often driven by simple goals: increasing safety and improving firefighters' ability to protect property and provide life-saving work each day.
From increasing operational efficiency to enhancing community connection, Pierce listens to the voices of firefighters and works continuously to develop solutions for those on the front-lines.
What are some of the key trends fire departments are talking about in 2024 and beyond?
1. Fleet Standardization: Streamlining Operations and Maintenance
Increased call volumes and mileage are driving the growing trend toward fleet standardization—the practice of manufacturing fire trucks according to consistent specifications, layout and/or configurations.
Fleet standardization offers many benefits to departments including:
- Streamlining operations with consistency among apparatus
- Creating maintenance efficiencies
- Improving training and safety knowledge
- Providing faster access to parts and service
- Providing cost savings based on a more efficient order process and repeatable manufacturing
While fleet standardization is on the rise, there's a parallel increase in the customization of each apparatus to maximize operational function.
The balance between standardization and customization is a continuous evolution in the industry—making the most out of each apparatus, ensuring every aspect of its design and function serves a purpose and ultimately, enhancing the efficiency and effectiveness of fire departments.
2. Innovations in Safety and Cleanliness
The increasing focus on safety and cleanliness in fire apparatus design is a direct response to the needs and concerns of firefighters.
Safety Systems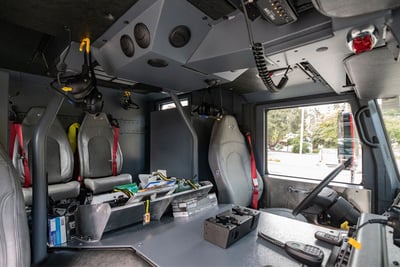
Manufacturers are integrating passive and active safety systems into truck designs and are educating firefighters about them.
- Passive safety systems include seat belts and frontal and side roll airbags. They remain dormant until a collision occurs, after which they react to protect the vehicle's occupants.
- Active safety systems, such as tire pressure monitors, anti-locking brakes and auto-traction, always operate and continuously collect real-time data to enhance vehicular safety.
Cleanliness
The 'clean cab' concept aims to reduce firefighters' exposure to harmful carcinogens and toxins by removing contaminants from the cab. This can be achieved in various ways, like using easily cleaned seating materials, like leather or vinyl; replacing rubber flooring with diamond plate or by keeping gear, such as SCBAs, out of the cab.
Each department must determine if and when to transition to safety-focused and cleaner concepts, but many are integrating elements in new apparatus to create an environment which promotes firefighters' long-term health and well-being.
3. Electrification: A New Era in Fire Apparatus Design and Functionality
There has been a marked shift toward emission reduction in various sectors in recent years and the fire industry is no exception. The push for cleaner, more environmentally friendly apparatus has been gaining momentum, driven by the dual goals of improving operational safety and reducing environmental impact.
The introduction of electric vehicles (EVs) to fire department fleets is still in its infancy, but Pierce battery technology shows strong reliability for use in extended firefighting operations. After all, firefighters can't afford to worry about whether or not the water will flow when they need it most.
Take, for example, the experience of Portland Fire and Rescue operating a Pierce® Volterra™ Pumper. Responding to a four-alarm fire, the Pierce Volterra Pumper seamlessly transitioned from electric to internal combustion engine power without any noticeable changes in water pressure or operational performance. Furthermore, the truck was able to drive the crew back to the station on EV power, demonstrating the potential for EVs to integrate smoothly into existing firefighting routines.
But the journey towards electrification isn't a race; it's about finding the most responsible, effective solutions.
The goal is to meet fire departments where they are, providing them with the tools they need to serve their communities without requiring them to drastically alter their methods or routines. This approach is being well received by customers, who appreciate the commitment to both environmental responsibility and operational efficiency.
Looking ahead, individual departments' long-term objectives will shape this trend's trajectory. Infrastructure considerations and local conditions will play a decisive role in determining the pace and extent of electrification. However, the willingness to adapt and overcome emission challenges is evident and the future of firefighting looks cleaner and more sustainable than ever.
Episode One of the Pierce Dispatch podcast dives into this topic in more detail. Learn more here and listen in!
4. Color Schemes: Enhancing Fire Truck Visibility, Branding and Community Identity
More than functional pieces of machinery, firetrucks are also symbols of community service, safety and pride. From color schemes to graphics, every aspect of a fire truck's design communicates something about the department it represents.
For example, the Hattiesburg Fire Department’s aerial ladder is painted purple to match local colors. In some cases, departments incorporate designs created by local students, further emphasizing their commitment to community engagement.
Painting a fire truck transforms it from a piece of machinery which performs a function effectively to a symbol resonating with the community it serves. As fire departments continue to innovate and adapt, we expect to see more creative, community-oriented designs on the roads.
5. Manufacturability and Efficiency: Pierce's Ongoing Efforts to Optimize the Manufacturing Process
As the industry sees growth and increases in legacy equipment replacement, fire departments grapple with procurement challenges and long lead times. Recently, the demand for fire apparatus has outpaced supply, resulting in an industry-wide backlog, forcing many departments to re-evaluate their procurement strategies, adjust their forecasting strategies and consider fleet standardization.
To address these issues, Pierce has introduced several initiatives to optimize the manufacturing process without compromising on quality.
- The Build My Pierce™ program was launched at a time when customers were seeking new ways to expedite the order process. The BMP™ program has fostered a partnership between the customer and the dealer, facilitating more rapid construction and delivery of new vehicles.
- Another Pierce-driven program, “lane strategy,” involves sending trucks down different lanes based on option content and order frequency. This approach has been instrumental in speeding up the manufacturing process.
These efforts reflect Pierce's commitment to meeting customer needs and adapting to the changing landscape of the fire industry. By investing in innovative solutions and rethinking traditional processes, Pierce is helping departments navigate procurement challenges and reinforcing its reputation as a reliable manufacturing partner in the fire service.
Listen in to Episode One of the Pierce Dispatch podcast, which covers these trends in depth with cohosts Alie Reetz and Dan Meyer.
What trends are you seeing in the fire industry right now? Let us know in the comments.